MAE4340: Innovative Product Design
Ithaca, NY
Ithaca, NY
biGrip

Fall 2019
In Fall 2019, I (in a group of 7 MAE seniors) ideated, designed, and prototyped the ‘biGrip’, an ergonomic grip designed for the elderly and those with mobility or dexterity issues.
The biGrip was created to allow gripping of any implement by joints that cannot be entirely curled, and will guide the user’s fingers to the specific optimal position through a simple visual guide. It is designed for a wide variety of grip and hand sizes, as well as any shape of implement to be gripped, due to the use of an inflatable bladder as the internal adaptable gripping mechanism. The biGrip’s innovative shape allows the same tool to be used for both the internal and external precision grips.
Calling our group ‘Squoval’, we worked through the design process from beginning to end: we performed empathy fieldwork to identify real-world challenges by speaking to the elderly ourselves, and synthesized this knowledge using systems engineering tools to create problem statements defining the scopes of possible products. We then created looks-like and works-like prototypes, modeled the shape in clay, 3D-scanned it into CAD, and used a Formlabs Form 2 and Stratasys Objet to print the shell. After assembling and presenting the final prototypes, we created a manufacturing guideline to show the path ahead in mass-producing biGrips, as well as completed preliminary patent paperwork to learn more about the IP process.
The biGrip was created to allow gripping of any implement by joints that cannot be entirely curled, and will guide the user’s fingers to the specific optimal position through a simple visual guide. It is designed for a wide variety of grip and hand sizes, as well as any shape of implement to be gripped, due to the use of an inflatable bladder as the internal adaptable gripping mechanism. The biGrip’s innovative shape allows the same tool to be used for both the internal and external precision grips.
Calling our group ‘Squoval’, we worked through the design process from beginning to end: we performed empathy fieldwork to identify real-world challenges by speaking to the elderly ourselves, and synthesized this knowledge using systems engineering tools to create problem statements defining the scopes of possible products. We then created looks-like and works-like prototypes, modeled the shape in clay, 3D-scanned it into CAD, and used a Formlabs Form 2 and Stratasys Objet to print the shell. After assembling and presenting the final prototypes, we created a manufacturing guideline to show the path ahead in mass-producing biGrips, as well as completed preliminary patent paperwork to learn more about the IP process.
MAE3780: Mechatronics
Ithaca, NY
Ithaca, NY
Cyclops
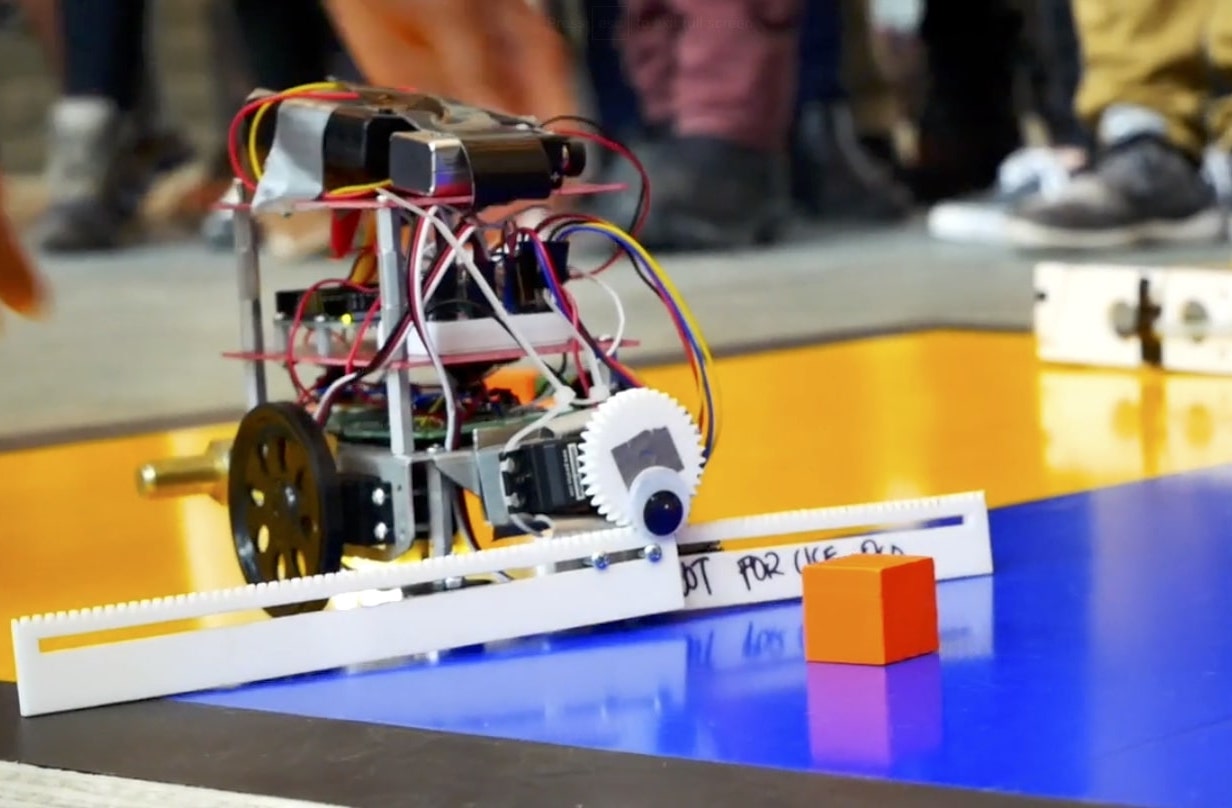
Fall 2018
The final project of Cornell’s Mechatronics class is the Cube Craze competition- students design and build a robot capable of pushing 1” wood cubes onto the opponent’s side of a playing field. The winner is the team with fewer cubes left on their side than the opponent’s after 60 seconds.
Our team of 3 created a robust robot with an actuated rack-and-pinion mechanism to increase pushable area. Allowing a compact form factor to expand into a larger shape ensured that even if pins were disconnected and the mechanism did not work, our robot would still be able to function effectively in competition. We were not allowed to use the Arduino IDE, and had to hard-code motion planning and sensor checks in C to ensure our robot was not exceeding the bounds of the board.
Because of the reliability of our robot, we reached the semi-finals of Cube Craze and earned the maximum amount of extra credit possible in the competition.
Our team of 3 created a robust robot with an actuated rack-and-pinion mechanism to increase pushable area. Allowing a compact form factor to expand into a larger shape ensured that even if pins were disconnected and the mechanism did not work, our robot would still be able to function effectively in competition. We were not allowed to use the Arduino IDE, and had to hard-code motion planning and sensor checks in C to ensure our robot was not exceeding the bounds of the board.
Because of the reliability of our robot, we reached the semi-finals of Cube Craze and earned the maximum amount of extra credit possible in the competition.
MAE2250: Mechanical Synthesis
Ithaca, NY
Ithaca, NY
Piston-based Water Pump
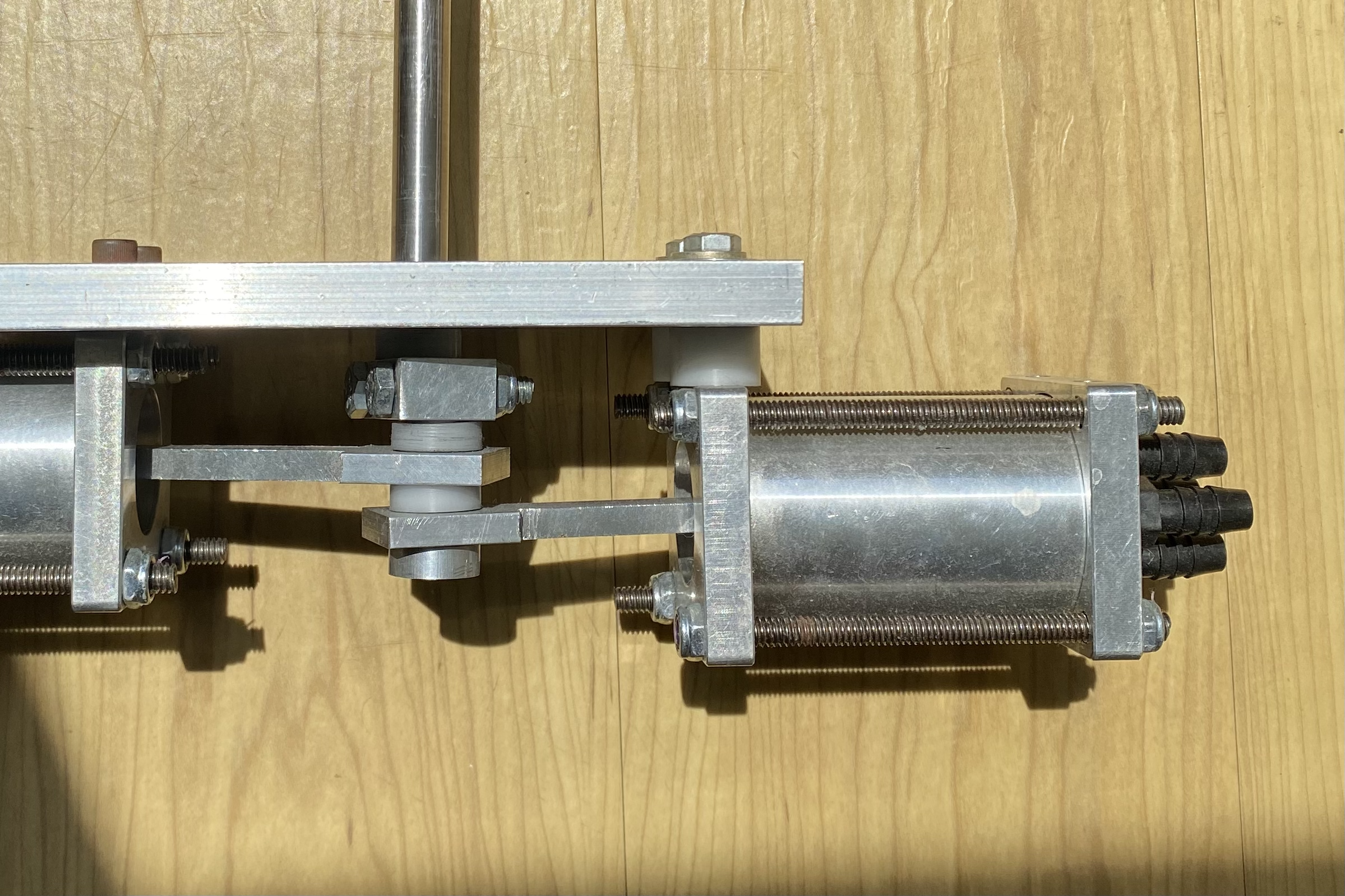
Spring 2018
As part of MAE2250: Mechanical Synthesis, students are expected to design, manufacture, and test a pump that is capable of pumping at least 1 liter of water within 60 seconds.
My role on a group of 6 was to design the pump in CAD using Fusion 360, as well as take the lead on machining necessary components. We built a crankshaft-style double-piston pump and pumped nearly 6 liters using it. One of the challenges of deciding on a piston pump was preventing seizing- we made the call early on to sacrifice a bit of travel to make the piston head thicker and make the pump foolproof. Between using Delrin (acetal resin) for the piston heads and a great machining job done by the group, our pump was capable of being operated by hand- no other pump in the class that year was.
My role on a group of 6 was to design the pump in CAD using Fusion 360, as well as take the lead on machining necessary components. We built a crankshaft-style double-piston pump and pumped nearly 6 liters using it. One of the challenges of deciding on a piston pump was preventing seizing- we made the call early on to sacrifice a bit of travel to make the piston head thicker and make the pump foolproof. Between using Delrin (acetal resin) for the piston heads and a great machining job done by the group, our pump was capable of being operated by hand- no other pump in the class that year was.