Verkada
San Mateo, CA
San Mateo, CA
Hardware Engineering Program Manager

[coming soon]
Lucid Motors
Newark, CA
Newark, CA
Vehicle Integration Engineer

I joined Lucid Motors, a rapidly growing EV startup, in July 2021 as a mechanical engineer on the Vehicle Integration team. Along with my colleagues, I helped take new vehicles from the concept development stage to production.
I was responsible for defining and owning customer-centric requirements for vehicle attributes across Lucid, tracking engineering progress and ensuring our products meet our customers’ needs and expectations. This involved working cross-functionally with our different attribute engineering teams and, for some attributes, developing verification and validation plans myself.
I also worked with our Program Management, Engineering, Software, Manufacturing, and Design teams to create Build plans for the Lucid Gravity SUV’s various prototype phases; along with timelines and quantities, this involved defining the vision and scope for each build while being as efficient as possible with our resources to meet all conflicting needs.
I was responsible for defining and owning customer-centric requirements for vehicle attributes across Lucid, tracking engineering progress and ensuring our products meet our customers’ needs and expectations. This involved working cross-functionally with our different attribute engineering teams and, for some attributes, developing verification and validation plans myself.
I also worked with our Program Management, Engineering, Software, Manufacturing, and Design teams to create Build plans for the Lucid Gravity SUV’s various prototype phases; along with timelines and quantities, this involved defining the vision and scope for each build while being as efficient as possible with our resources to meet all conflicting needs.
SharkNinja
Needham, MA
Consumer Product Development Intern,
Needham, MA
Consumer Product Development Intern,
Shark R&D
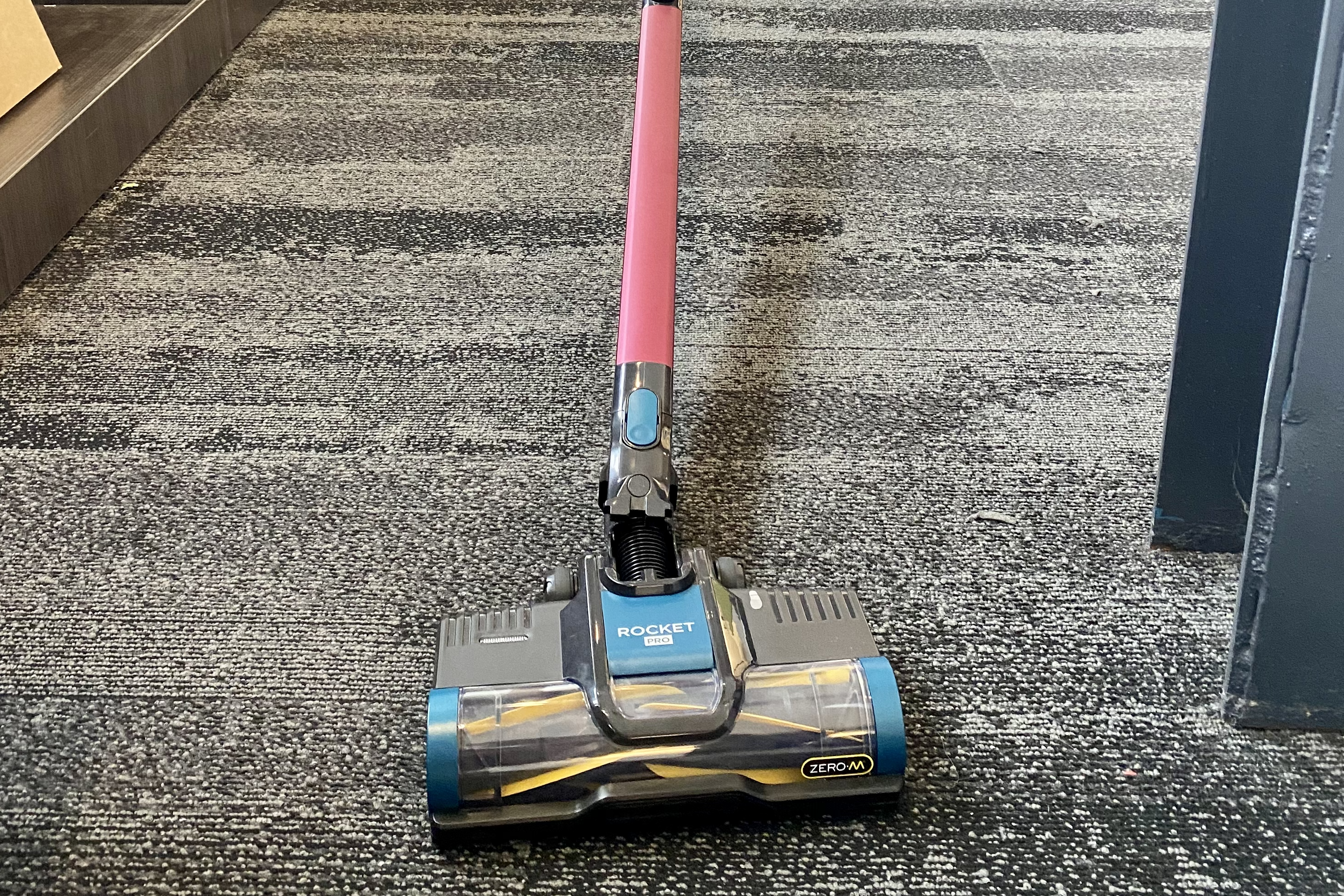
From June to December 2020, I interned at SharkNinja, a leading manufacturer of home appliances, in Needham, MA. I was a Consumer Product Development Intern on the Shark R&D team, taking new products from the prototype stage to mass-manufacturing.
During my internship, I led early-stage development on specific product features for some of Shark’s 2021 offerings- this involved iteratively designing, prototyping, and testing parts and assemblies. Some of this work ended up on a filed patent application that I am listed as an inventor on, and the nozzle was launched in the Japanese market as the EVOPOWER System.
My role also involved creating and executing testing plans (DOE) to diagnose current product issues with the goal of performing running changes to existing SKUs. Lastly, I worked with the Operations team as well as prototyping vendors and OEMs to improve SharkNinja’s in-house and purchased rapid prototyping capabilities.
The EVOPOWER System was launched in Japan in October 2021- I helped develop the floor nozzle, whose advanced single-brushroll design allows effective suction of debris of varying sizes across all floor types in a lightweight, maneuverable footprint ideal for the global vacuum market.
During my internship, I led early-stage development on specific product features for some of Shark’s 2021 offerings- this involved iteratively designing, prototyping, and testing parts and assemblies. Some of this work ended up on a filed patent application that I am listed as an inventor on, and the nozzle was launched in the Japanese market as the EVOPOWER System.
My role also involved creating and executing testing plans (DOE) to diagnose current product issues with the goal of performing running changes to existing SKUs. Lastly, I worked with the Operations team as well as prototyping vendors and OEMs to improve SharkNinja’s in-house and purchased rapid prototyping capabilities.
The EVOPOWER System was launched in Japan in October 2021- I helped develop the floor nozzle, whose advanced single-brushroll design allows effective suction of debris of varying sizes across all floor types in a lightweight, maneuverable footprint ideal for the global vacuum market.
Markforged
Watertown, MA
Watertown, MA
Materials Print Intern

In Summer 2019, I interned at Markforged, a leading manufacturer of metal and composite 3D printers, as part of their Materials team.
While at Markforged, I created the DOE for an extensive study looking into filament compatibility with Markforged’s lineup of composite 3D printers. This involved use of testing equipment for dynamic mechanical analysis, tensile testing, and rheology, among others. I also assisted in development of Onyx ESD, an Onyx chopped-fiber filament variant with static-dissipative properties, as well as created and redesigned software and hardware tools used internally within the Materials team to improve efficiency.
While at Markforged, I created the DOE for an extensive study looking into filament compatibility with Markforged’s lineup of composite 3D printers. This involved use of testing equipment for dynamic mechanical analysis, tensile testing, and rheology, among others. I also assisted in development of Onyx ESD, an Onyx chopped-fiber filament variant with static-dissipative properties, as well as created and redesigned software and hardware tools used internally within the Materials team to improve efficiency.
Invacare
Elyria, OH
Elyria, OH
Engineering Intern, Global Power Engineering
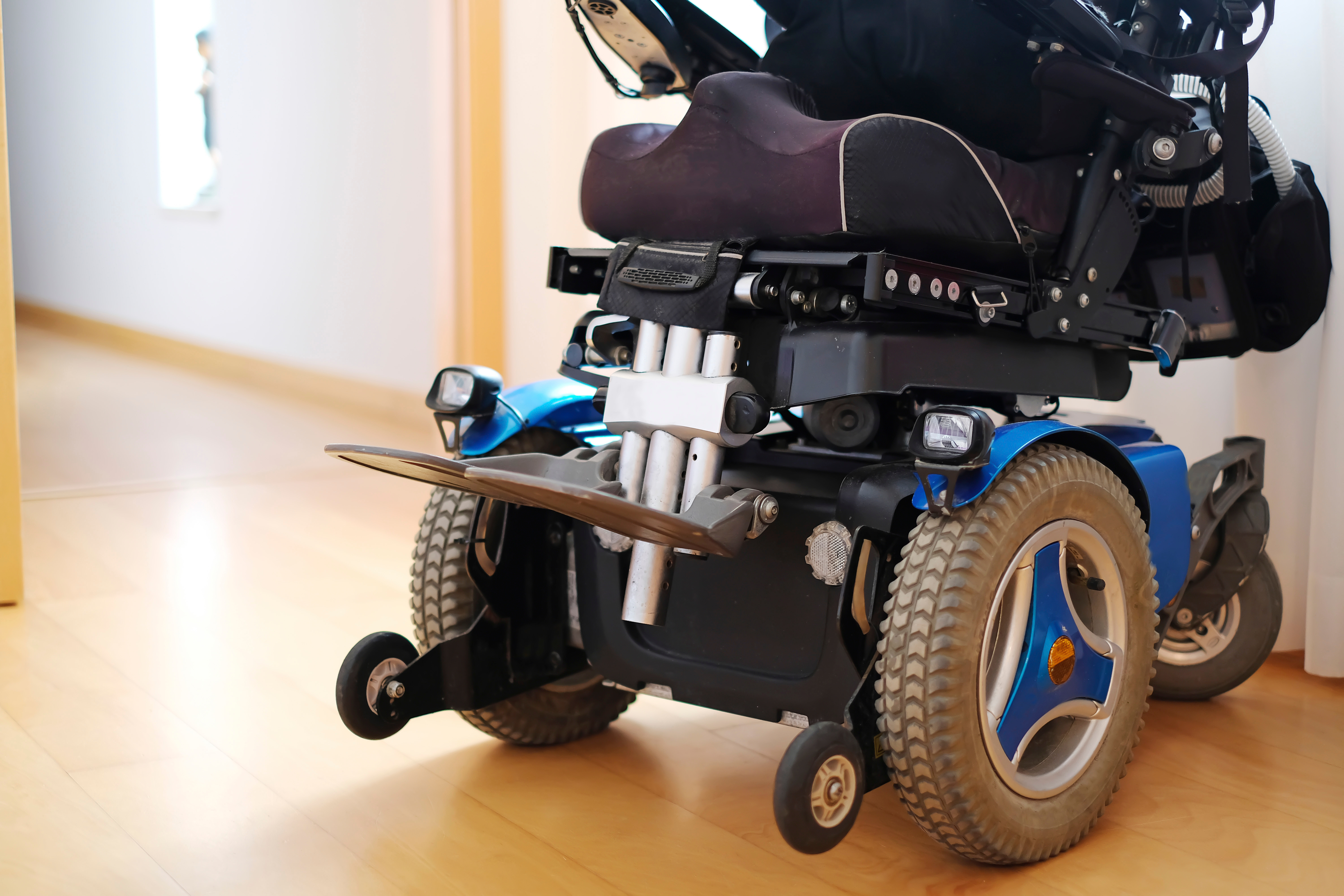
In Summer 2018, I interned at Invacare Corporation (NYSE: IVC), a leading manufacturer of non-acute medical devices, as part of the Concept Engineering team on the Global Power Engineering group.
While at Invacare, I assisted in the mechanical design and prototyping of a new low-cost, modular power wheelchair, complying with FDA regulations, to enter manufacturing starting mid-2019. I also helped design potential solutions to constrain vital components to pass the ANSI/RESNA standard 20G crash test, and worked with the QA team to investigate drive motor testing plans after import.
While at Invacare, I assisted in the mechanical design and prototyping of a new low-cost, modular power wheelchair, complying with FDA regulations, to enter manufacturing starting mid-2019. I also helped design potential solutions to constrain vital components to pass the ANSI/RESNA standard 20G crash test, and worked with the QA team to investigate drive motor testing plans after import.
Cornell Rapid Prototyping Laboratory
Ithaca, NY
Ithaca, NY
Lab Manager / Research Assistant
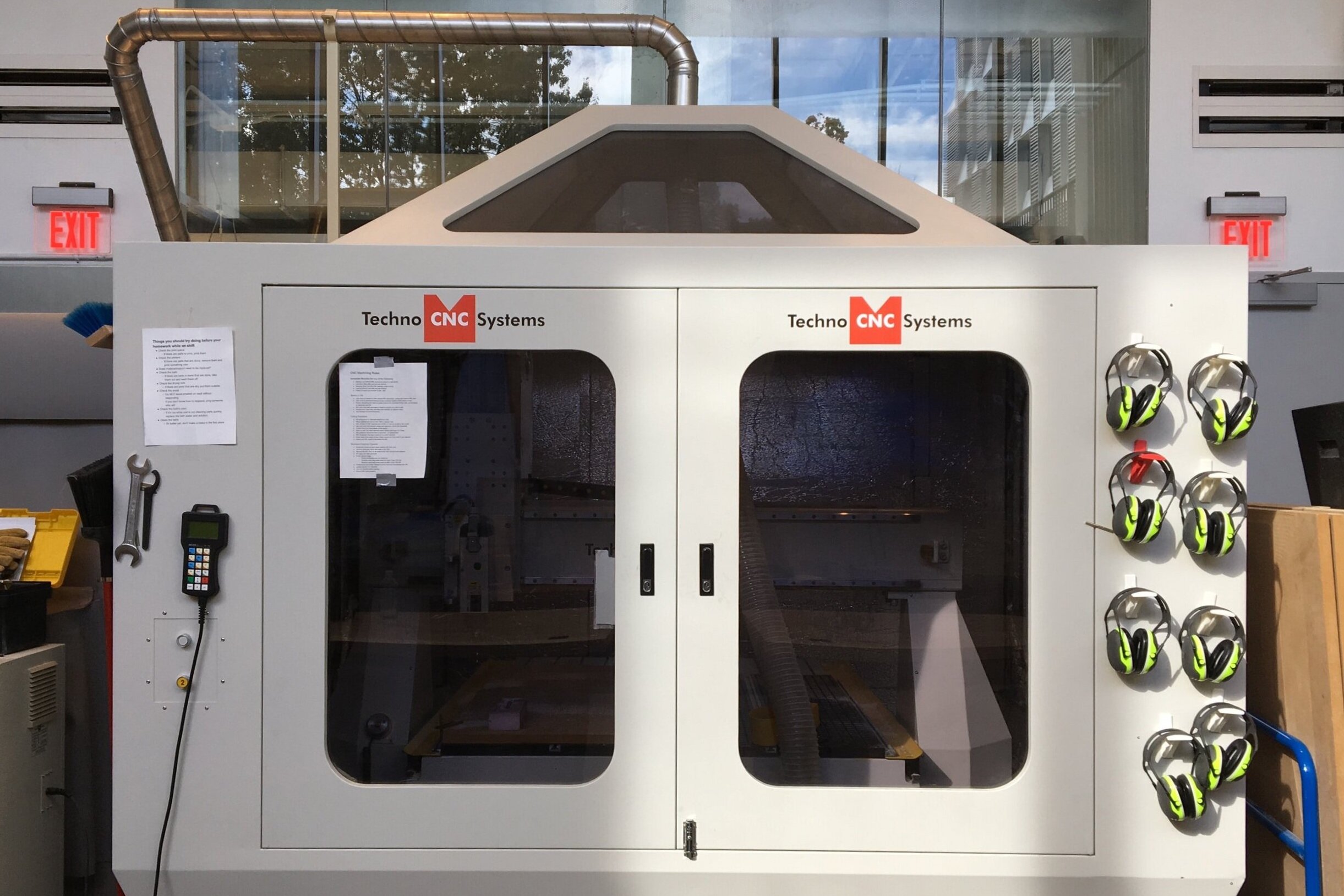
The Rapid Prototyping Laboratory (RPL) is an entirely student-staffed makerspace catering to engineering project teams and Cornell Engineering classes. RPL has ten 3D printers from industry pioneers like Stratasys, Markforged, and Formlabs, among others, as well as two laser cutters and one CNC router.
I worked at RPL as a student employee from January 2018 to May 2021, and ran the lab from May 2019 onwards. As student employees, we were responsible for the upkeep and throughput of the equipment in the Lab, as well as acting as consultants, working with students to better design their parts and expanding the knowledge of rapid prototyping methods on campus.
As a co-Lead, I supervised a dozen student employees and was responsible for increasing the efficiency of the Lab and its equipment, working closely with MAE department staff.
I worked at RPL as a student employee from January 2018 to May 2021, and ran the lab from May 2019 onwards. As student employees, we were responsible for the upkeep and throughput of the equipment in the Lab, as well as acting as consultants, working with students to better design their parts and expanding the knowledge of rapid prototyping methods on campus.
As a co-Lead, I supervised a dozen student employees and was responsible for increasing the efficiency of the Lab and its equipment, working closely with MAE department staff.
Cornell Baja SAE Racing
Ithaca, NY
Ithaca, NY
Suspension and Ergonomics Subteams
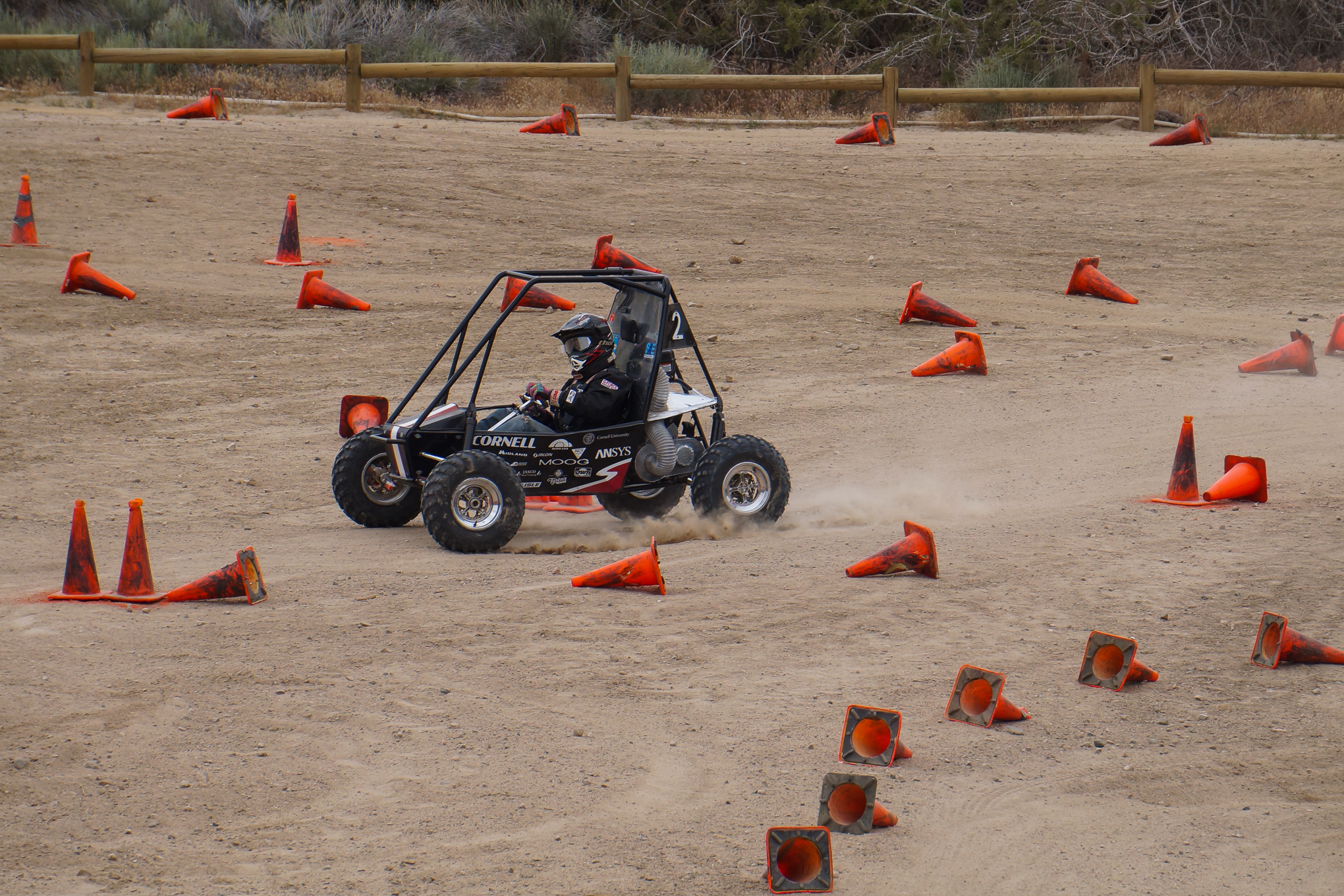
As a member of the Cornell Baja Racing team for almost the entirety of my college years, I’ve been involved in the design, analysis, manufacturing, testing, and racing of offroad cars at many Baja SAE competitions.
While on the Suspension subteam, I designed the front and rear uprights, ball joint assemblies, and welding fixtures. As a member of the Ergonomics subteam, I was responsible for the material selection, design, and manufacture of the body panels and steering wheel assembly, as well as overall fabrication of various ergonomic components using advanced manufacturing methods.
We have done well competitively, consistently placing in the Top 5 over all three annual competitions in several seasons, among a playing field of 100+ international collegiate teams.
While on the Suspension subteam, I designed the front and rear uprights, ball joint assemblies, and welding fixtures. As a member of the Ergonomics subteam, I was responsible for the material selection, design, and manufacture of the body panels and steering wheel assembly, as well as overall fabrication of various ergonomic components using advanced manufacturing methods.
We have done well competitively, consistently placing in the Top 5 over all three annual competitions in several seasons, among a playing field of 100+ international collegiate teams.
OD17 (2021 Competition Season)
Fabrication Assistance, General Morale Boosting
OD16 (2020Competition Season)
Body Panels and Materials, Advanced Manufacturing, Ergonomics System Goals, Mentoring
M15 (2019 Competition Season)
Front Upright, Ball Joints
M14 (2018 Competition Season)
Rear Upright
OD13 (2017 Competition Season)
Suspension Link Fixtures
Fabrication Assistance, General Morale Boosting
OD16 (2020
Body Panels and Materials, Advanced Manufacturing, Ergonomics System Goals, Mentoring
M15 (2019 Competition Season)
Front Upright, Ball Joints
M14 (2018 Competition Season)
Rear Upright
OD13 (2017 Competition Season)
Suspension Link Fixtures
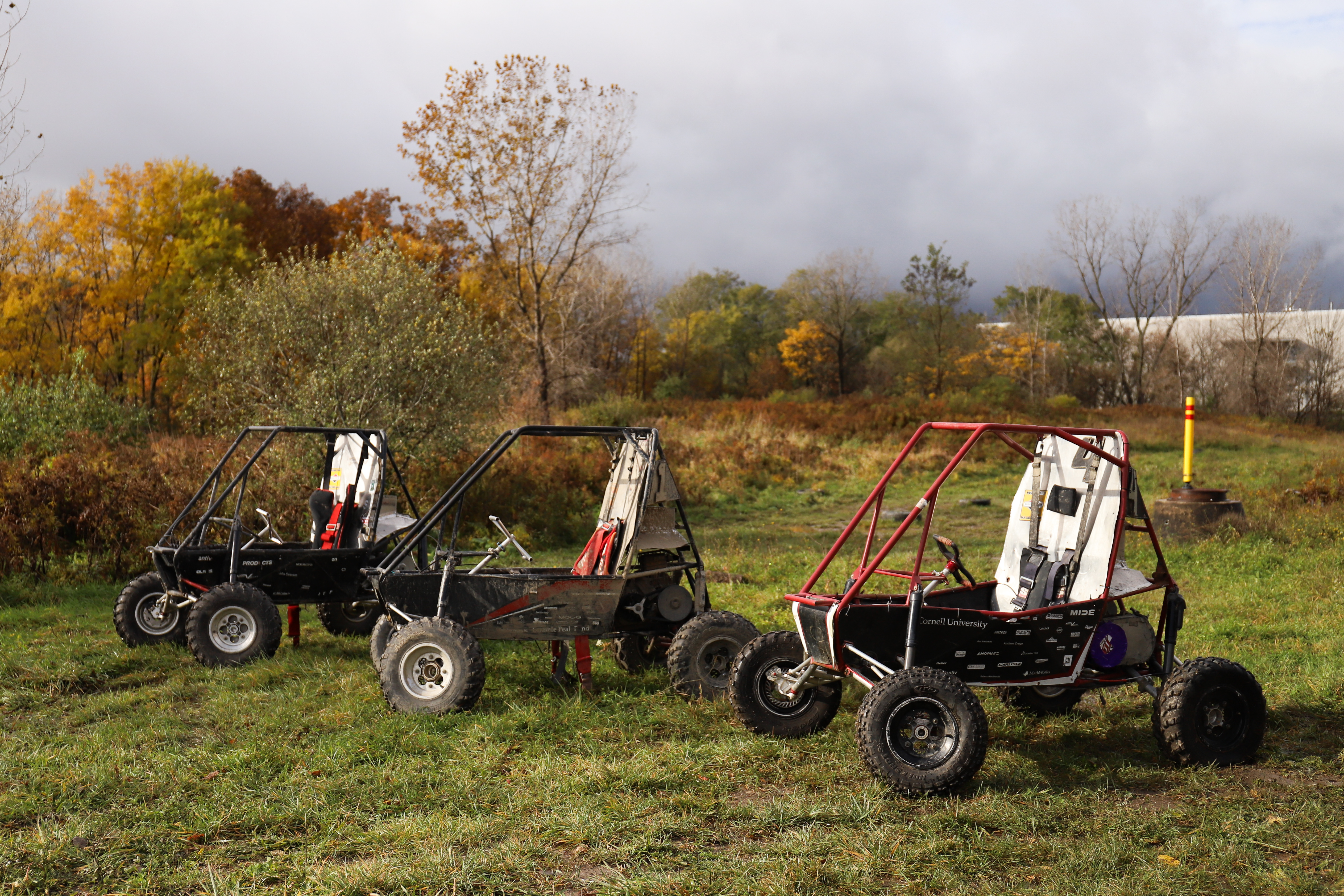
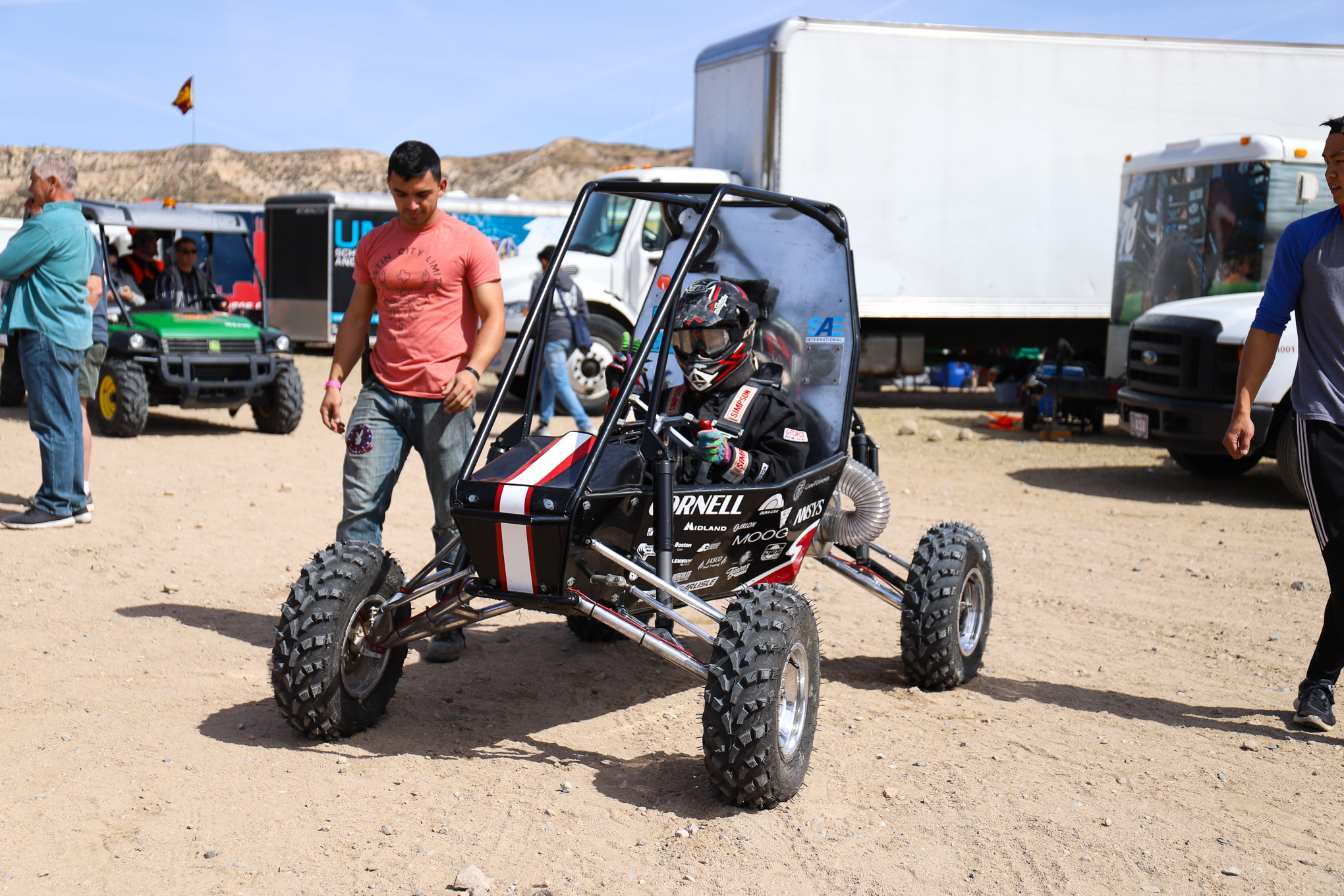